Basic Info.
Product Description
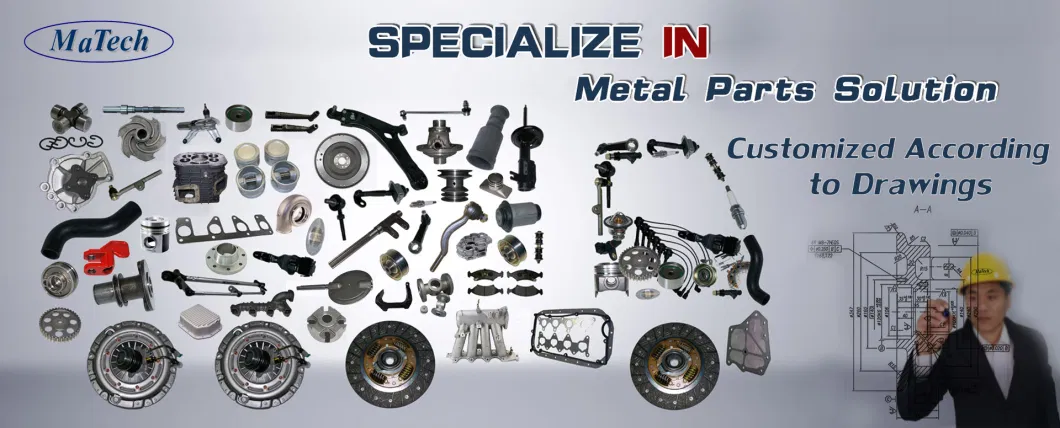
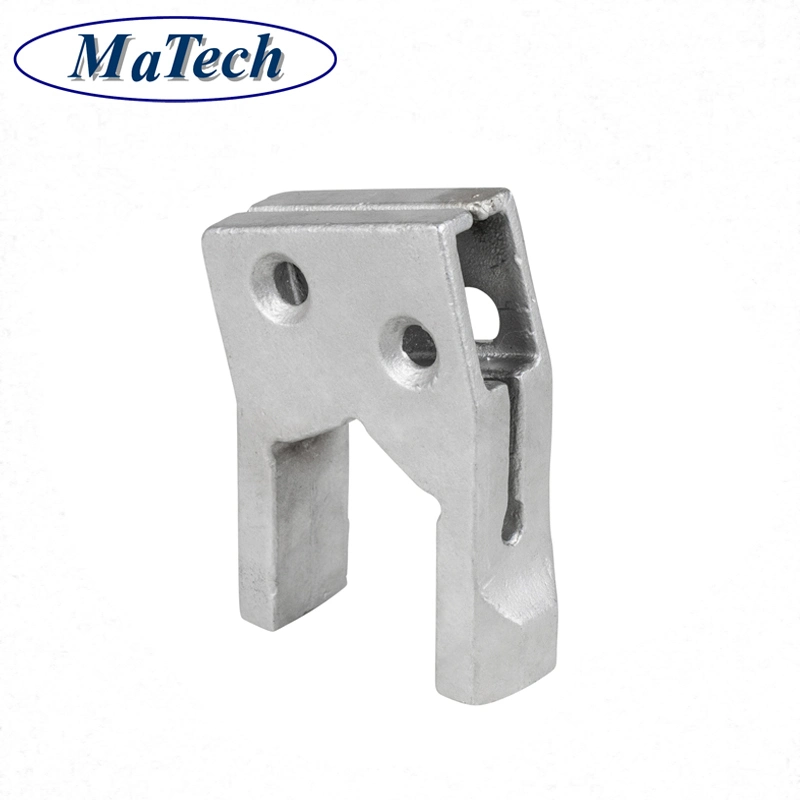
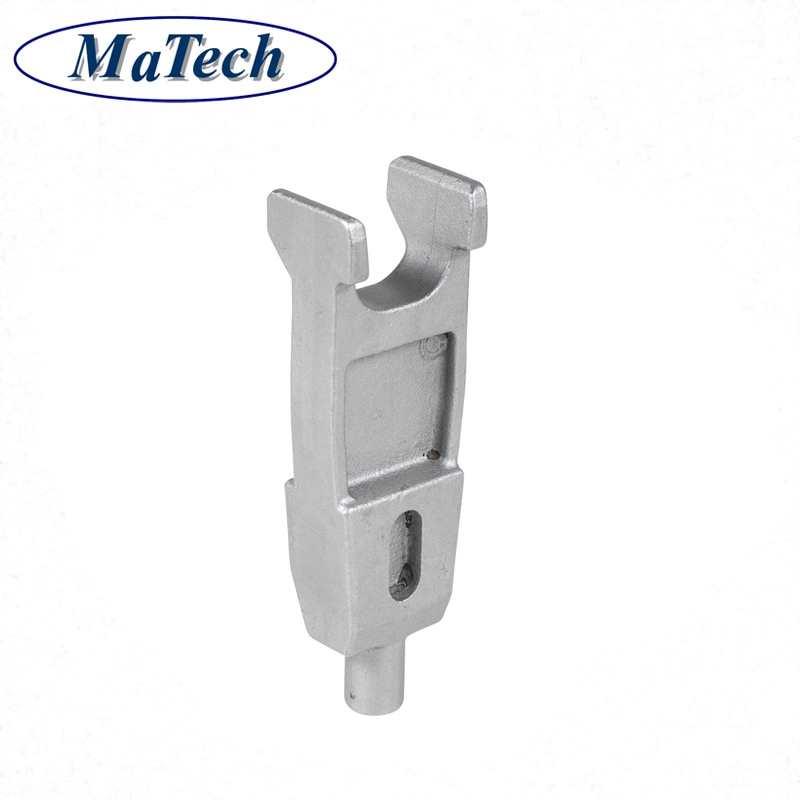
Item Name | Customized Processing Heat Resistant Stainless Steel Lost Wax Casting Auto Parts |
General Products Application/Service Area | Metal Parts Solution for Vehicle, Agriculture machine, Construction Machine, transportation equipment, Valve and Pump system, Agriculture machine metal Parts, engine bracket, etc. |
Main blank Process for Steel Casting | Investment casting (wax mold made by middle temperature wax) /Precision casting ; Lost Wax Casting (wax mold made by low temperature wax)/ Precision casting |
Blanks Tolerance -Casting Tolerance | CT7-8 for Lost wax Casting Process CT4-6 for Investment casting Process |
Applicable Material | Carbon steel, Low Carbon steel, middle carbon steel,WCB, WCA, WCC, ISO 340-550, Alloy Carbon steel: G25CrMo4, Heat Resistant Steel, Stainless Steel: CF8, CF8M, . G-X6CrNiMo1810, G-X7CrNiNb1189, SUS 304, 304L, 316, 316L. OR According to customer requirement |
Casting Blank Size /Dimensions | 2 mm-600mm / 0.08inch-24inch according to customer requirement |
Casting Blank Weight | Range from 0.01kg-85kg |
Applicable Machining Process | CNC Machining/ Lathing/ Milling/ Turning/ Boring/ Drilling/ Tapping/ Broaching/Reaming /Grinding/Honing and etc. |
Machining Tolerance | From 0.005mm-0.01mm-0.1mm |
Machined Surface Quality | Ra 0.8-Ra3.2 according to customer requirement |
Applicable Heat Treatment | Normalization , annealing, quenching and tempering, Case Hardening, Nitriding, Carbon Nitriding, Induction Quenching |
Applicable Finish Surface Treatment | Shot/sand blast, polishing, Surface passivation, Primer Painting , Powder coating, ED- Coating, Chromate Plating, zinc-plate, Dacromat coating, Finish Painting, |
MOQ | For stainless steel casting : 200pcs For machining: 50pcs |
Lead Time | 45days from the receipt date of deposit for Lost Wax Casting |
Products shown here are made to the requirements of specific customers and are illustrative of the types of manufacturing capabilities available within MATECH group of companies. MATECH policy is that none of these products will be sold to 3rd parties without written consent of the customers to whom the tooling, design and specifications belong.
Product Profile
1. Marterial percentage | alloy steel:45% carbon steel:35% stainless steel:10% iron:10% |
2. Casting weight percentage | 0.1-5kg:40% 5-20kg:30% 20-40kg:20% above 40kg:10% |
3. Industry percentage | Components for train & railway: 25% Components for automobile & truck: 30% Components for construction machinery & forklift: 25% Components for agricultural machinery: 10% Other machinery compponents: 10% |
4. Globa market share | United States:30% Europe:35% Japan& Korea:15% Domestic market:15% Other:5% |
5. Production capacity | Production Capacity: 20,000 tons / year The Current Production Output: 15,000 tons / year Open Capacity Percentage: 25% |
Manufacturing Process
Process design⇒ Tooling making ⇒ Wax injection ⇒Wax pattern assembly⇒ Mold preheat ⇒ Wax removal ⇒Stuccoing ⇒Dipping Casting⇒ Mold shake out ⇒Work piece cut-off ⇒ Grinding ⇒ Pack& transport ⇒ Final inspection ⇒Machining ⇒ Heat treatment
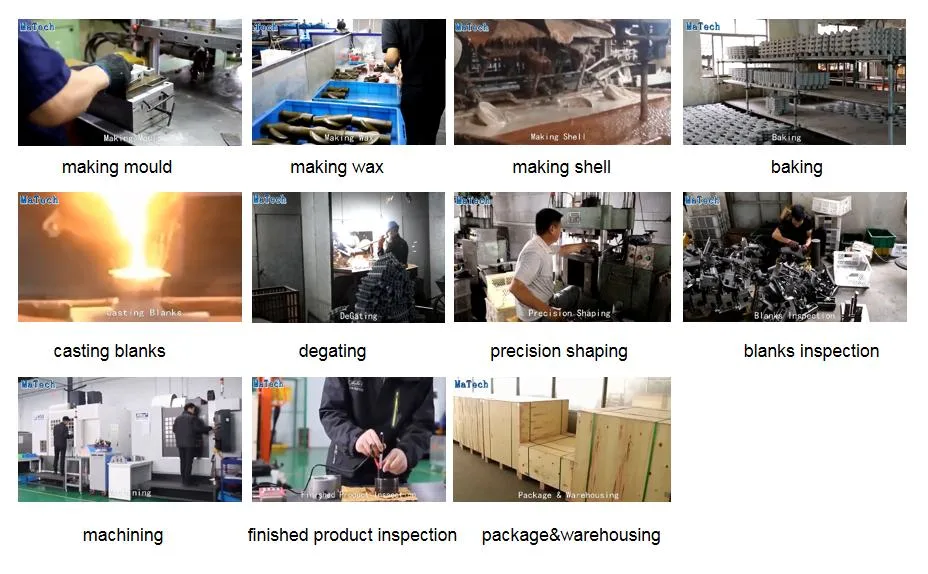
APQP and Inspection Report
APQP-Casting 1. Process Flow Diagrams 2. Control Plan 3. Process FMEA 4. Casting Process Instruction 5. Solidification Simulation Report 6. Heat Treatment Work Instruction 7. Casting Final Quality Control WI 8. Visual Inspection VI For Surface Irregularities | Inspection Report-Casting 1. Material Test Report(A) 2. Material Test Report(B) 3. Magnetic Particle Inspection Report 4. Ultrasonic Examination Report 5. Radiographic Test Report 6. Destructive Test Report 7. Coating Test Report 8. Visual Inspection Report 9. Casting Inspection Report |
APQP-Machining 1. Process Flow Diagrams 2. Control Plan 3. Process FMEA 4. Machining Process Instruction 5. Gauge List And Validation Plan 6. Final Quality Control | Other Quality Document 1. PPAP Checklist 2.Measurement System Analysis Study 3. Process Capability Studies 4. Corrective Action Report(8D) 5. Packaging Instruction |
Inspection Report-Machining 1. Dimensional Inspection Report(A) 2. Dimensional Inspection Report(B) 3. CMM Report |
Key Testing Equipment
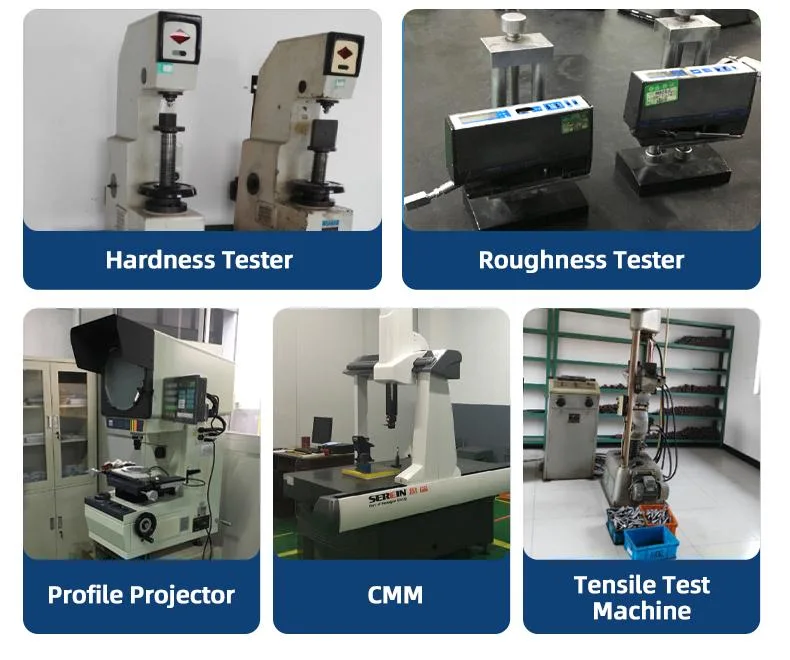
Application | |||||
• Agricultural equipment | • Armament | • Automobile industry | • Computing equipment | • Medical / dental instruments | • Measuring instruments |
•Miscellaneous equipment | •Pharmaceutical industry | • Orthopedic implants | • Safety equipment | • Petrochemical industry | • Industrial valves |
•Fixing and movable equipment | • Sanitary fittings | • General machinery | • Pumps and general connections | • Food and beverage processing | • Instrumentation equipment |

Technical Support:
Shanghai Matech is professional at independent development and design. Our engineers are skilled at AUTO CAD, PRO ENGINEER, SOLID WORKS and other 2D & 3D softwares. We are able to design, develop,produce and deliver your PO according to your drawings, samples or just an idea. Dural control of standard products and OEM products.
Quality Control:
1) Checking the raw material after they reach our factory------- Incoming quality control ( IQC)
2) Checking the details before the production line operated
3) Have full inspection and routing inspection during mass production---In process quality control(IPQC)
4) Checking the goods after they are finished---- Final quality control(FQC)
Factory show
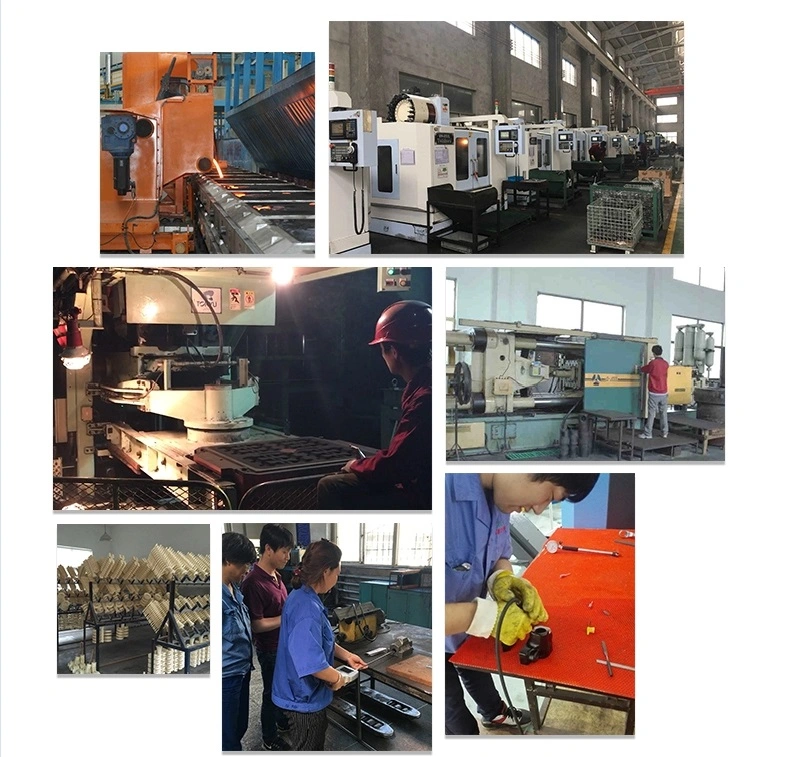
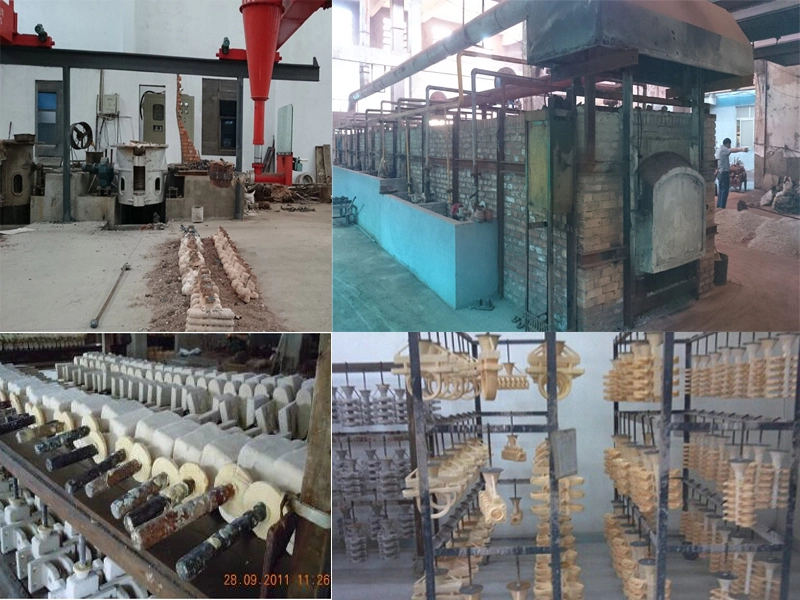
--Branch of Matech Industry Ltd.
We specialize in Metal Parts Solution for Vehicle, Agriculture machine, Construction Machine, transportation equipment, Valve and Pump system.
With keeping manufacturing process design, quality planning, key manufacturing processes and final quality control in house.
We are mastering key competence to supply quality mechanical parts and assembly to our customers for both Chinese and Export Market.
To satisfy different mechanical and functional requirements from our customers we are making a big range of metal products for our clients on base of different blanks solutions and technologies.
These blanks solutions and technologies include processes of Iron Casting, Steel Casting, Stainless Steel Casting, Aluminum Casting and Forging.
During the early involvement of the customer's design process we are giving professional input to our customers in terms of process feasibility, cost reduction and function approach.
You are welcome to contact us for technical enquiry and business cooperation.
Our Team
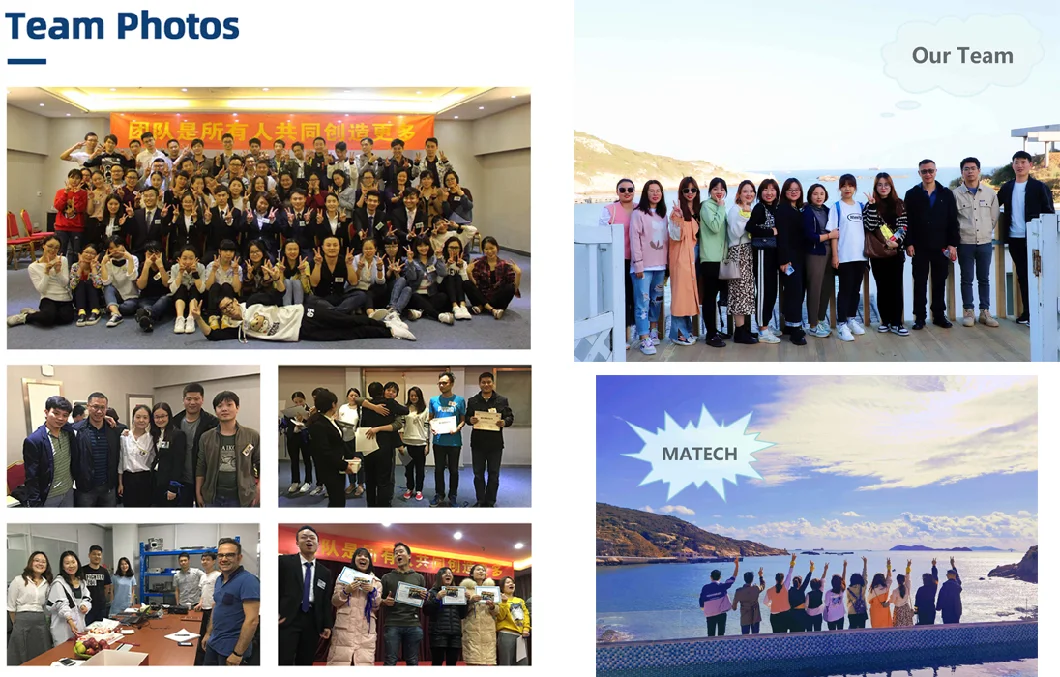
Why Choose Us ?
1. Over 15 years professional manufacture experience. → We know better to your needs.
2. One-stop Service of Custom mold design from Initial drawing design, Material selection assistance, Mold structure/Mold flow analysis, Trial & mass production to Final assembly & shipment. → To ensure you get finished products with good assembly function.
3. High skilled and well-trained working team under good management environment. → To make sure high quality of your products.
4. Large and strong production capacity. → To meet your high demands very well.
5.Best price based on same quality requirements. →To help your project with most economical solution.
6. We have very strict quality control process as below. → To deliver the qualified products for you.
In coming Quality control (IQC) : All incoming raw material are checked before used.
In process quality control (IPQC) : Perform inspections during the manufacturing process.
Final quality control (FQC) : All finished goods are inspected according to our quality standard for each products.
Outgoing Quality Control (OQC) : Our QC team will 100% full inspection before it goes out for shipment.
7.Reliable Package & flexible in-time delivery. →To guarantee the product are well received in your side.
8. 24 hours on-line service with quick response. → To support your any inquiry or question.
Customer photos
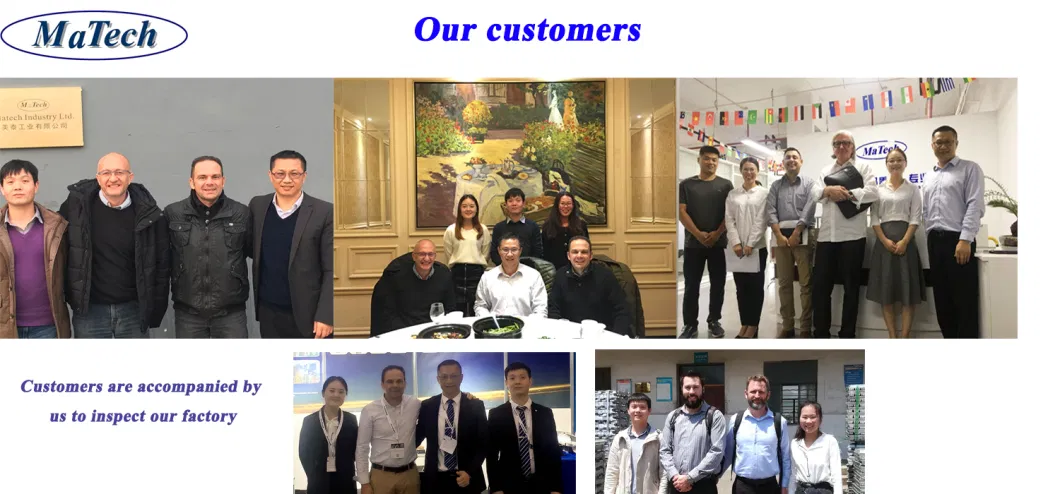
Core Competence
Advantages 1:High Engineering and Technical Capability
* Based on customer needs, in the beginning of product development, offer a solution, casting design, by structural component designed to casting parts, optimize the product design, then reduce costs and creating the more value for the customers.
* Special Techniques Enable us to Be Competent with Those Difficulties at Wax Injection & Shell Making Procedures When Manufacturing the Parts with Inner-Sophisticated-Structures.
* Use casting simulation analysis system software, try our best to ensure the success of the one-time trial sample.
* IQC, IPQC and FQC quality management team to control the whole production process, effectively prevent the generation of unqualified product.
* Our casting' PPM ≤1000 Machining ' PPM ≤600
* We sticks to the quality management philosophy that "Starting from the customer needs and ending with their satisfaction,focusing on customer demands and exceeding their expectations"
* Quotation, Quality Complaints and Email Response can usually be quickly and efficiently feedback within 48 hours.
* We have carried out an information-based management which is driven by an ERP and PMC system, to ensure on time delivery rate:95%
* MATECH has completed a transformation and upgraded to a deep-processing manufacturer with expanded production capabilities and is committed to be equipped with other capabilities except casting, we focus on developing terminal products for top-end markets.
* High technical content in machining, and casting with sheet metal, welding, assembling, MATECH has the most competitive advantage, it is the good choice for you.
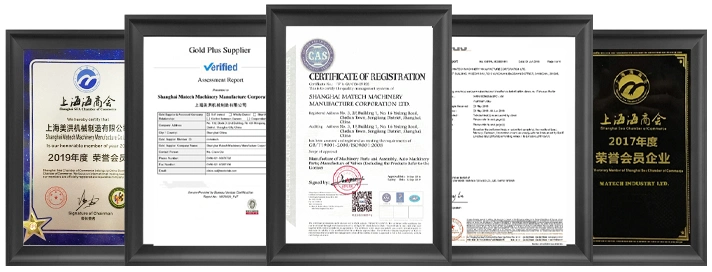
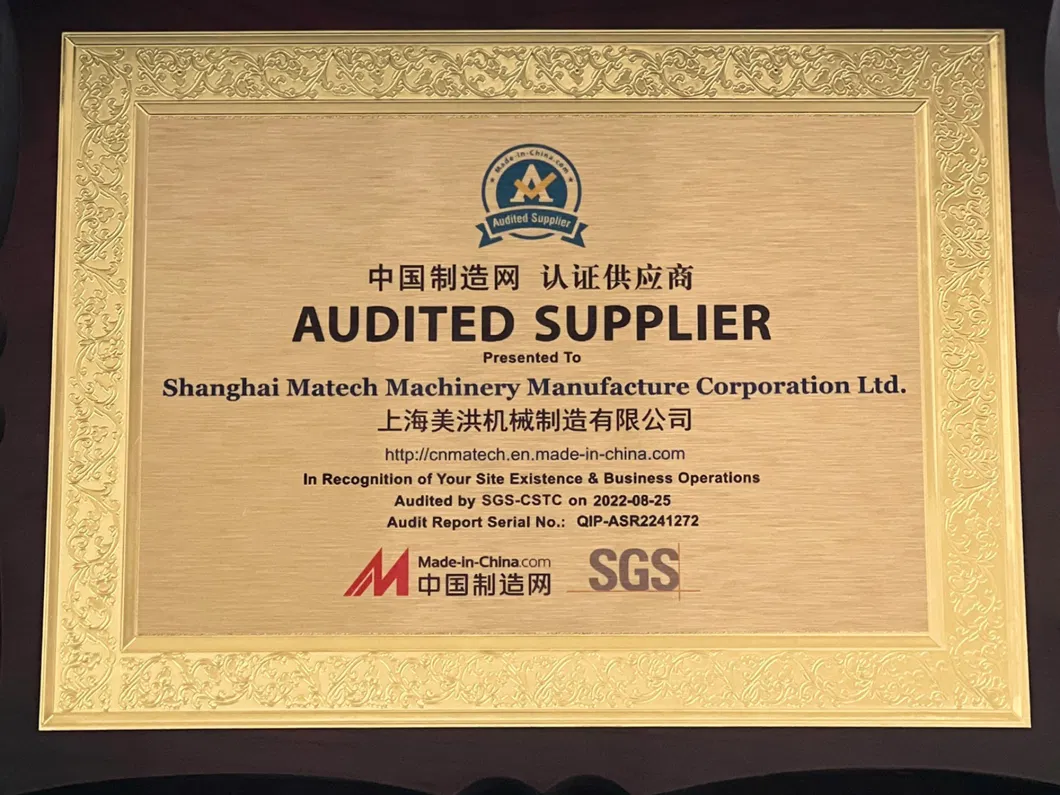
Packaging & Shipping
1, Bundles Packing: Inside: packed with plastic protective film to protect each piece. Outside: Wrap to be bundles by waterproof
craft paper or EPE film.
2, Carton Packing: Inside: Each pcs pack in one plastic bag. Outside: Numbers of quantity put in one carton.
3, Wood Pallet Packing: Inside: Bundles or cartons packing; Outside: Numbers of bundles or cartons laden on one wood pallet.
4, Customized Packing As Clients Request is Available.

1. Are you a manufacturer or a trading company?
3. Can you make casting according to our drawing?
4. Can you make casting based on our samples?
5. What's your quality control device in house?