Basic Info.
Model NO.
as requirement
Various Material and High Performance
More Than 30-Year Experience
Trademark
CIC
Origin
China
Product Description
Product Description
Wear-Resistant Mill Liner with Different Materials for Grinding Equipments
Casting & forging ability
CITICHL is the casting & forging center in central-south China, possessing 50t electric arc furnace, 60t LF ladle refining furnace, and 60t VD/VOD refining furnace, etc. We can pour 350t liquid steel one time and yields more than 200,000t of high quality liquid steel and can produce the high quality steel of more than 260 steel grades such as carbon steel, structural alloy steel and the structural steel, refractory steel and stainless steel of special requirement. The maximum weight of casting, gray casting, graphite cast iron and non-ferrous casting is 200t, 30t, 20t and 205t separately.
The company is the forging center in central-south China. It is very powerful in forging. The single free forging is 100t(max weight). We can roll rings of different sections of carbon steel, alloy steel, high temperature alloy and non-ferrous alloys such as copper alloy, aluminum alloy and titanium alloy. The maximum diameter is 5.5m and single piece of the forging weighs 10t. We have 8400t, 3150t, 1600t, water press and RAW 200/160-5000/750 large-size ring mill of high precision in Asia made in WAGNER, Germany.
Heat treatment ability
The company is the heat treatment base in national machinery trade in central and south China, possessing Φ3×1.6m carburizing furnace, Φ2.3×17m,Φ2.3×9.5m shaft furnace, 8.5×13m,5×15m,6×14.5m,4.5×18m automatic controlled car type heat treatment furnace group. We can supply the quenched and tempered part over 45t, the carburizedand quenched gear and pinion below 20t, shaft≤5.7m in length and the induced girth ring diameter≤5m
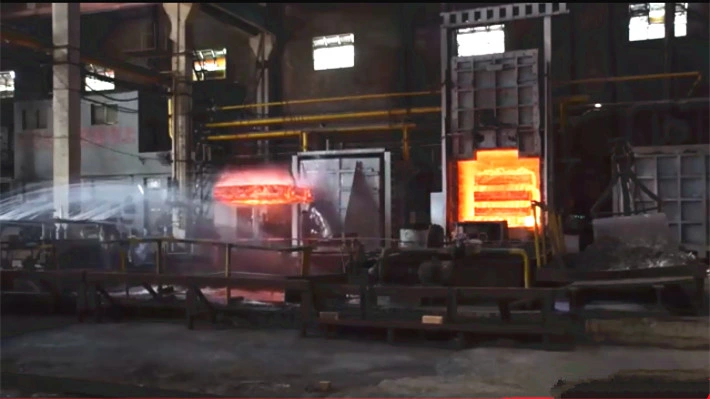
CITICHL is experienced in manufacturing large-sized marine castings and forgings, possessing advanced technology, strong technical force and completes testing facilities, it has the ability to manufacture and develop all various marine parts. CITICHL is the earliest approved enterprise for manufacturing marine castings and forgings by Britain Lioyd's Register of Shipping(LR), Japan Shipping Classification Society(NK), Norway Shipping Classification Society(DNV), France Shipping Classification Society(BV), Germany LIoyd(GL), American Bureau of Shipping(ABS), Registro Italiano Navale (RINA) and China Classification Society of Shipping(CSS).
Main marine castings and forgings Products:
Steel castings (below 200t per piece): stern, stern tube,the overall and fission rudder, etc.
Steel forgings (below 70t per piece): propeller shaft, couplings, intermediate shaft, rudder stock, rudder pintle , bolt and nut, etc.
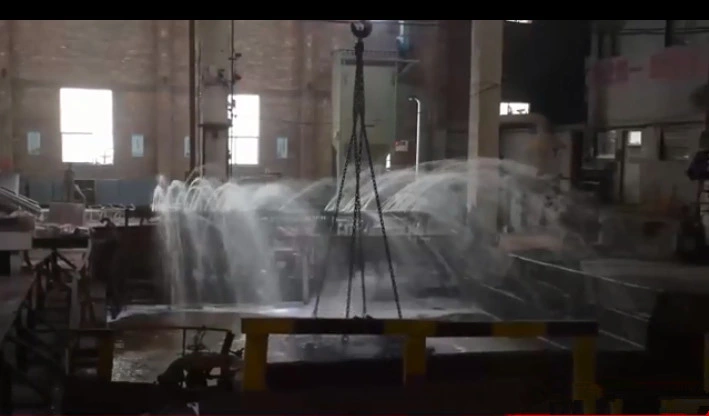
Features:
l Material: High Manganese Steel, Super-High Manganese Steel, High Chromium Casting Iron, Alloy Steel, Chromium-molybdenum Steel, Low Carbon Steel, or as per the customer requests.
l Hardness: as per your request.
l Impact Value: as per your request.
l Tensile Strength: as per your request.
l Heat Treatment Process: Normalizing, Tempering, Quenching & Tempering.
l Surface treatment: rust preventive oil, or as per your requests.
l Process: raw material purchasing - casting- rough machining - heat treatment - semi-machining - finish machining - painting and packing. Various process conditions are available.
l Standard: ANSI, API, ASTM, BSI, DIN, GB, ISO, JIS.
l QA and DOC: Chemical Composition Report, Mechanical Properties Report, Spheroidization Rate Report, UT Report, PT Report, Heat Treatment Report, Dimensions Check Report, Hardness Report and etc.
l Quality Control: UT Test, MT Test, Visual Inspection, Third Party Inspection, Customer On-site Inspection.
Advantages:
l More than 30 years experience
l ISO9001:2008 Standard certified
l Custom-made design
l High abrasion resistance
l Long service duration
l Easy and fast installation and replacement
l OEM and ODM are available.
Packing:
l Seaworthy packing, or as required.
HMCB04 New Type Chromium-molybdenum Steel Linings
HMCB04 New Type Chromium-molybdenum Steel Mill Liners are a kind of new liners self-improved by CIC. With better performance and property than the common mill liners, HMCB04 Chromium-molybdenum Steel Mill Liners have won great reputation from the final users.
Performance Comparison
____ | HMCB04 Chromium-molybdenum Steel | Common Chromium-molybdenum Steel |
Hardness | HB 350-400 | HB350-375 |
Impact Value | ≥80J | ≥45J |
Tensile Strength | ≥1300J | ≥1200J |
Competitive Advantages:
l Self-improved property
l Of longer service life
l Of higher hardness
l Of better property of impact value and tensile strength
l Of higher hardenability
l Widely used and commonly accepted
l OEM and ODM are available.
Packing:
l Seaworthy packing, or as required.
With several decades of development, CIC has become the Manufacturing Base of Lining of Semi-autogenous Mills
1. Optimizing Manufacturing Process, Guarantee Lining Quality
Our high quality linings manufactured by advanced process have covered a wide marketing of semi-autogenous mills.
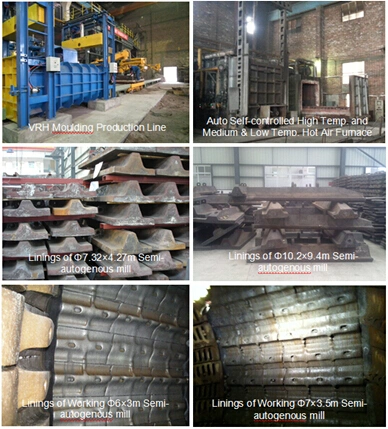
2. Optimizing Lining Design, Eliminating Break of Lining
A main working function of the lining is to lift the milling ball to a reasonable height, then fall along right rack and smash against the material enrichment area at the bottom of the mill in order to crush the material effectively. So it is greatly important of reasonable optimizing the lining design and correct guiding the milling ball running track in order that guarantee the optimized operation condition in the mill and effectively protect the shell lining of semi-autogenous mill, meanwhile, can eliminate lining break, prolong the service life and decrease effectively unit wear of linings and milling ball, and improve the hour production per machine.
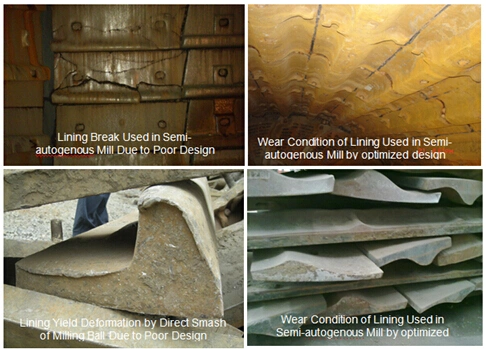
3. Focusing on Detailed Operating Condition, Improving Users' Benefits
Optimizing the lining design based on the wear forms of linings in different operating conditions maximally decrease the crashing function of the linings, and effectively decrease the weight of scrap linings. Improving the shape of linings can effectively improve the relative motion state between milling balls and linings, then decrease lining wear by material and milling balls and prolong the lining service life while reducing the users' production cost.
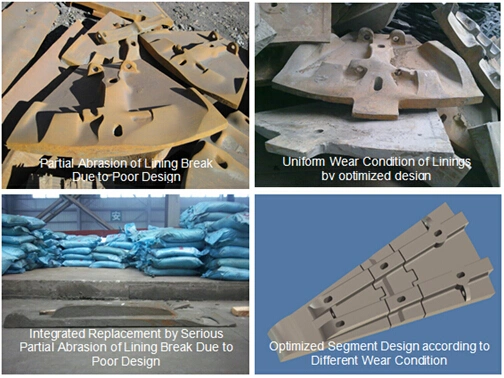