- Overview
- Product Description
- Working Principle
- Features
- After Sales Service
- FAQ
Basic Info.
Packaging & Delivery
Product Description
LECA Ceramsite Production Line Processing Plant
LECA consists of small, lightweight, bloated particles of burnt clay. The thousands of small, air-filled cavities give LECA its strength and thermal insulation properties. The base material is plastic clay which is extensively pretreated and then heated and expanded in a rotary kiln. Finally, the product is burned at about 1100°C to form the finished LECA product.
We could provide complete equipment for Light Expanded Clay Aggregate Production Line with capacity 15,000 to 300,000 m³/a, including the whole service of design, equipment/spare parts supply, investment consultation, installation and operation training for LECA Plant.
The main equipment in the LECA production line includes jaw crusher, mixing machine, ball mill, pelletizer, rotary dryer, trommel screen, rotary kiln, cooling machine. The main production steps of the LECA are including: crushing, mixing, grinding, pelletizing, calcining, cooling and screening. Hare are the detailed description.
1. Raw Material Process
The main raw material is clay or slurry. Building clay (or slurry) storage shell and flyash storage yard, we get the material by loader and do the proper mixing ration. And then the material will be fed into silo.When the clay size is too big, it should be crushed by roller crusher to get small size.
2. Mixing and Granulating
Set up an apron feeder under the hopper. Feed the material into a double shaft mixer. Then the material fall into a double roller granulator to become 5-10mm sphere shape material. And then they are fed to an insert type rotary kiln by belt conveyor.
3. Preheating and burning.
When the sphere shaper material enter into the preheating kiln by chute. The moisture will be dried and then the material will be fed into the burning kiln to become the Light Expanded Clay Aggregate (LECA) with bulk density of 500kg/m3.
4. Cooling
Light Expanded Clay Aggregate (LECA) outlet from the kiln will be fed into the cooler. Cooler shall adopt the single drum cooler, vertical cooler, grate cooler and etc.
5. Fuel Combustion
Coal, natural gas and biomass fuel are good choices as fuel.
6. Kiln Inlet Dust Collect
Gas from kiln inlet will be processed by air cooler machine and then sent to the bag filter for dedusting. And then it will be sent to the air.
7. Final Product Screening and Packing
The Light Expanded Clay Aggregate (LECA) outlet from rotary cooler and then fed into a vibration screen (or rotary screen). They will be screened into the size of 5mm, 15mm and 25mm. The different size will be packed in different bags, which will loaded for sales.
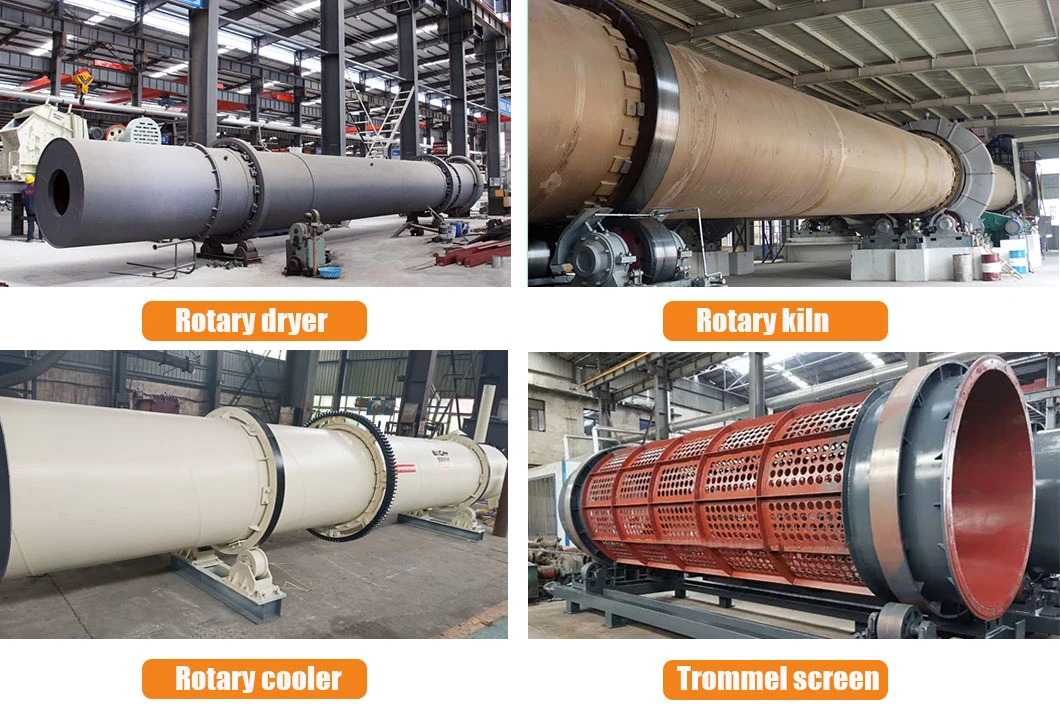
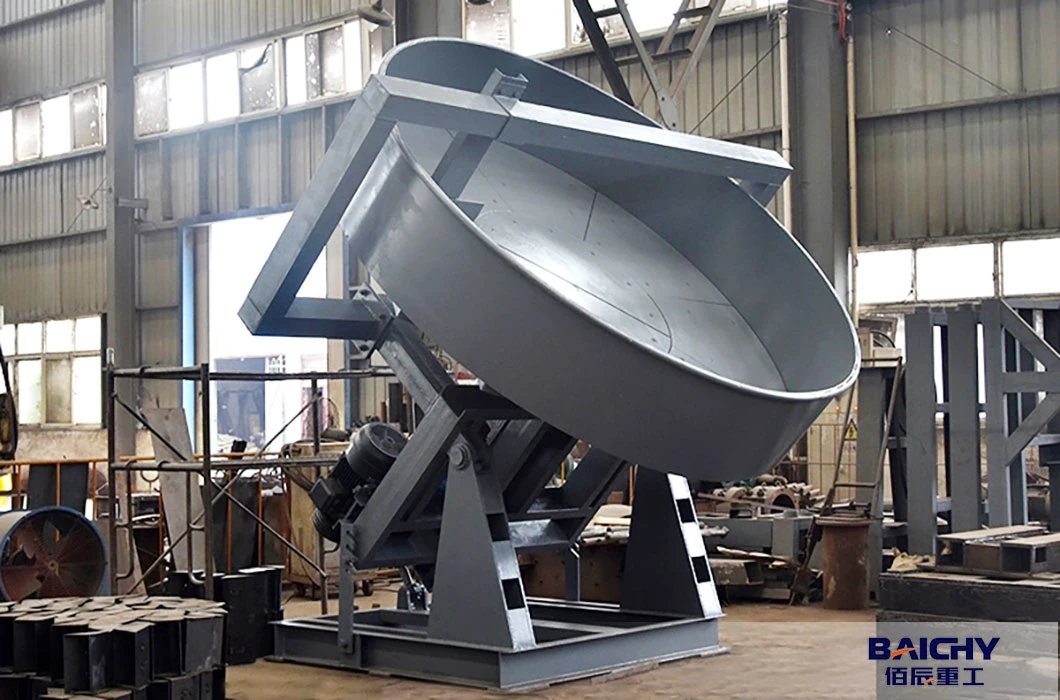
1. Energy-saving environment friendly
Advanced production process and large capacity for single production line with low heat loss. The advanced bag type dust collector, which is equipped in LECA equipment, keeps exhaust gas below 30mg/Nm3.
2. High degree of automation
Leca production line is fitted with temperature and pressure monitoring instrumentation, operating parameters of the computer display, and is capable of using advanced computer control to achieve automatic operation of the entire system.
3. Lost investment
Based on the features of Light Expanded Clay Aggregate (LECA), double-cylinder insert type rotary kiln controls the preheating and calcination process. The energy-saving vertical preheater is equipped in LECA production line with advanced process, and reasonable design and high level technology.
Pre-sale services:
(1) Advice of model choice.
(2) Design and manufacture machines according to customer's special requirements
(3) The company is free of charge to the user on-site engineering and technical personnel planning site for the user to design thebest processes and program
After-sale services:
(1) Arrange technicians to go to the site to guide installation
(2) If your machine is out of warranty period, Baichy could provide the spare parts.
(3) Complete sets of equipment installed, Baichy could arrange technical staff on-site for install, dubug and training until the user' satisfaction
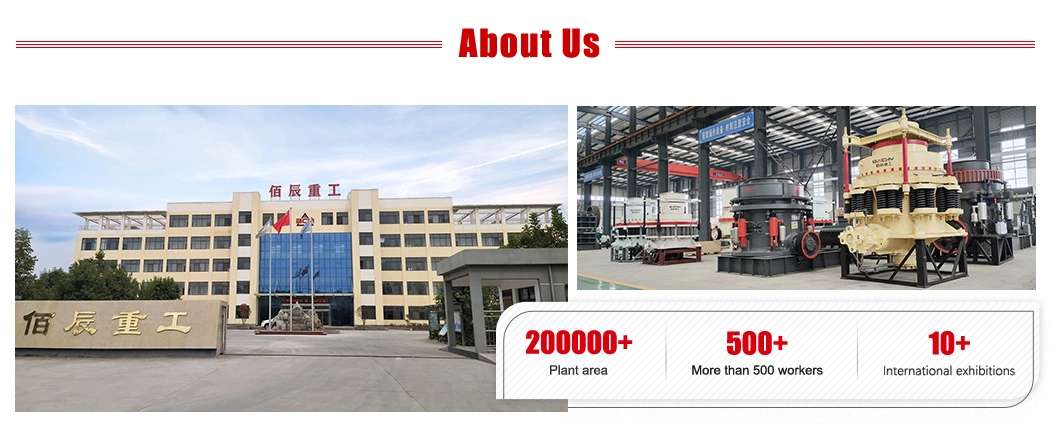
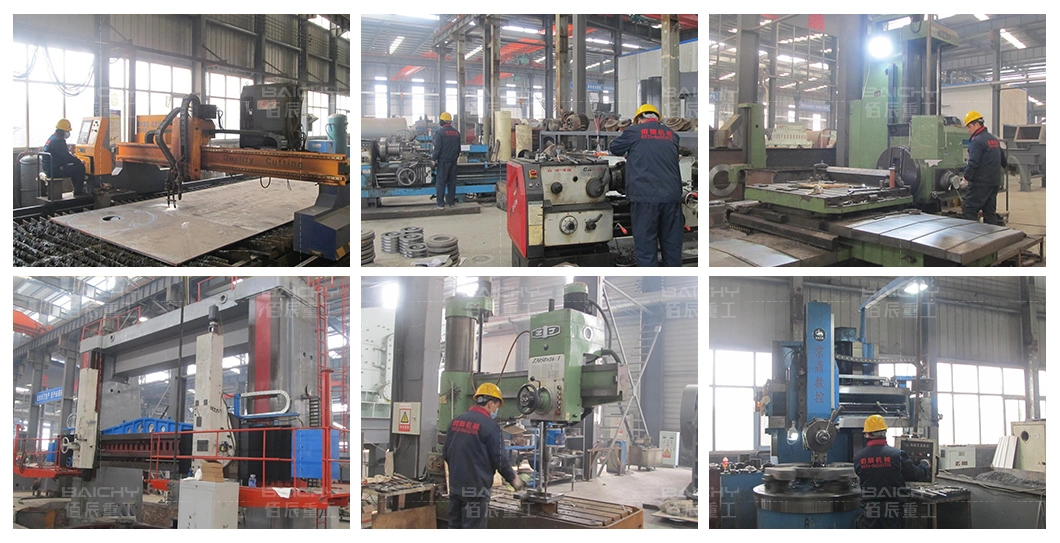
Baichy Factory
Headquarter of Baichy is located in Zhengzhou city, China and now we have two manufacturing bases as our strong support. One is located in Jiaozuo about 200,000 square meters, and the other is in Xingyang city, about 100,000 square meters.There are more than 200 sets of various large and medium-sized metal processing lathe, riveting machine, welding equipment and assembly equipment.
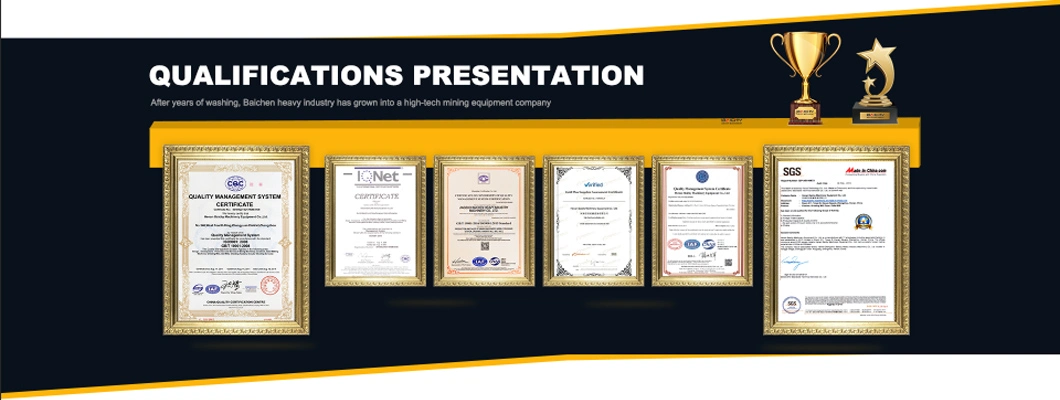
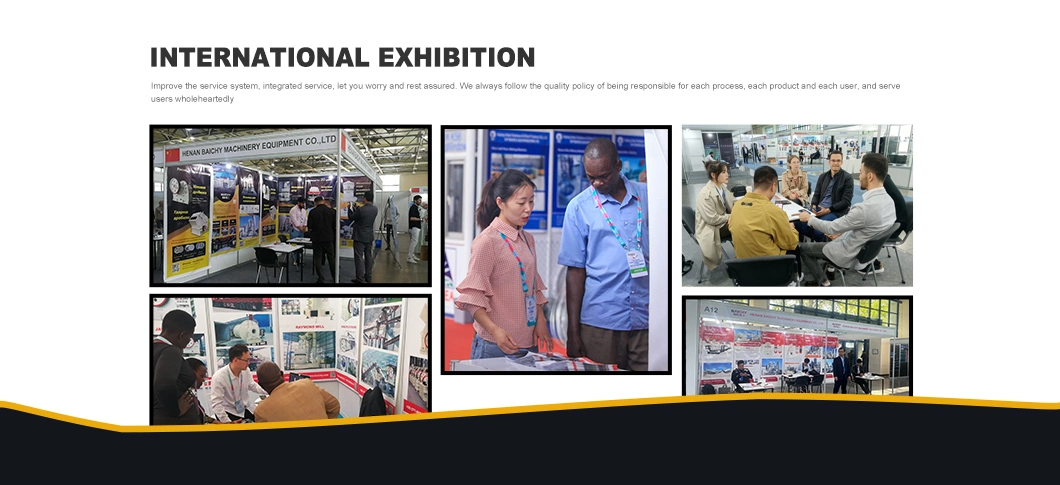
1. Are you manufacture or trading company?
We are factory, established in 2003.
2. How long is your delivery time?
7-10 days for the stock, 15-30 days for the mass production.
3. What is your payment method?
30% deposit in T/T advance, 70% balance before shipment.
4. How long is the warranty? Does your company supply the spare parts?
One year. Spare parts for you at lowest cost.
5. If I need the complete crushing plant can you help us to build it?
Yes, we can help you set up a complete production line and give you related professional advice. We had already build many mining projects in China & Overseas.